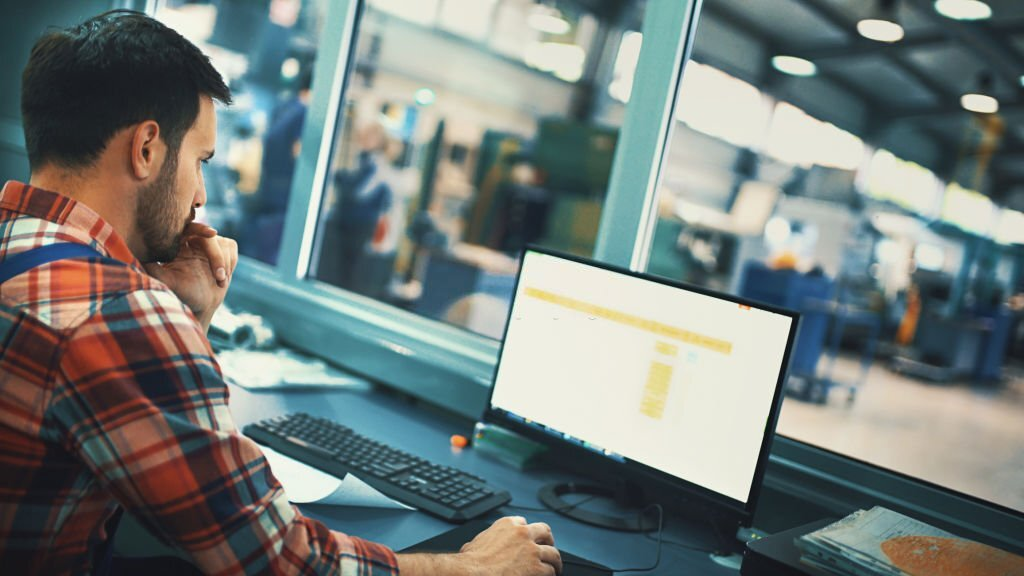
Tolerance analysis is integral to engineering, acting as a guardrail to ensure optimal system or product performance. It provides a means to understand how variations, such as part dimensions, assembly constraints, and manufacturing imperfections, could influence the functionality of a design. Through tolerance analysis, engineers can evaluate the acceptable deviations that uphold optimal operation and performance.
This tool is pivotal in many fields, including the automotive, aerospace, electronics, and industrial sectors. It empowers experts to pinpoint potential issues early in the design phase, saving valuable time and resources by avoiding expensive rectifications or manufacturing delays.
Moreover, tolerancing directly impacts the cost and performance of products. In devices where safety is paramount, such as electronic gadgets, tolerance analysis verifies whether the nominal clearances specified will meet safety requirements, considering the variability of manufacturing and assembly processes. In essence, tolerance analysis aids in the creation of superior, safer, and more efficient products that align with customer expectations.
Importance of tolerance analysis
There are some essential reasons why engineering needs tolerance analysis:
Understanding Machine Parts
Tolerance analysis holds a key role in defining machine parts. It ensures that all components can seamlessly work together, a crucial aspect for complex systems where numerous parts must perfectly align. Using tolerance analysis, engineers determine the optimal size of gaps, ensuring the assembly doesn’t require undue pressure or misalignment.
Boosting System Efficiency
The effectiveness of a product is significantly influenced by tolerance analysis. As changes in the dimensions of a system or object can alter its functionality, tolerance analysis enables engineers to identify potential issues that these variations may cause. Making necessary adjustments can prevent failures, mistakes, or premature wear and tear, enhancing the product’s durability and longevity.
Improving Production Processes
Tolerance analysis is a powerful tool to refine production processes. Engineers can devise more efficient manufacturing methods by understanding the permissible variations and their effects on the final product. This includes selecting suitable manufacturing techniques, setting realistic production targets, and minimizing waste and rework. Tolerance analysis, thus, enhances production efficiency, saving costs, and boosting productivity.
Cost Savings
Tolerance analysis is instrumental in reducing manufacturing costs. Engineers can minimize waste, rework, and production delays by analyzing tolerances and optimizing designs. Tolerance analysis facilitates time and cost savings by spotting potential issues early in the design phase.
Improved customer satisfaction
This analysis helps make products that customers love. By ensuring products work right and meet quality standards, engineers can ensure they meet customer needs. Happy customers often come from getting reliable, high-quality products.
Understanding Tolerance Analysis Methods
Engineers use several methods to ensure that parts of a product will fit together correctly, depending on the complexity of the design and the level of accuracy needed. The four standard methods are Worst-Case Analysis, Root Sum Squared (RSS) Analysis, Monte Carlo Simulation, and Statistical Analysis.
To better understand these complex calculations, our tolerance analysis tool can provide you with instant and accurate results.
Worst-Case Analysis
The Worst-Case Analysis involves figuring out the smallest and biggest possible sizes for each part. This helps to prepare for the best and worst scenarios, ensuring that all parts will still fit together. Engineers calculate these sizes by adding or subtracting the tolerances of all the parts from their nominal dimensions.
Applying these principles practically can be challenging. That’s why we’ve created the handy Stack-Up Tolerance Analysis Calculator to help you get a natural feel for how worst-case analysis works.
Derivation:
If we consider an assembly of n parts, where each part has a dimension ‘d’ and a tolerance ‘T’, the worst-case scenario for the largest dimension (Max) and smallest dimension (Min) are calculated as follows:
\colorbox{black}{$\textcolor{white}{\text{Max} = d_1 + T_1 + d_2 + T_2 + \ldots + d_n + T_n}$} \colorbox{black}{$\textcolor{white}{\text{Min} = d_1 - T_1 + d_2 - T_2 + \ldots + d_n - T_n}$}Statistical Analysis
The Statistical Analysis method uses statistics to predict how changes in part sizes might affect the final assembly’s size. It assumes that each part’s size follows a normal distribution (a bell curve), and the assembly’s overall size and variance are calculated based on these distributions.
Derivation:
If each dimension ‘d’ of a part follows a normal distribution with a mean ‘μ’ and a standard deviation ‘σ’, the total mean dimension (Mean) and the total standard deviation are calculated as follows:
\colorbox{black}{$\textcolor{white}{\text{Mean} = \Sigma \mu_i}$} \colorbox{black}{$\textcolor{white}{\sigma^2 = \Sigma \sigma_i^2}$}Root Sum Squared (RSS) Analysis
The Root Sum Squared (RSS) Analysis calculates the total tolerance by taking the square root of the sum of the squares of each part’s tolerance. This method is handy when dealing with many parts with unrelated and uncorrelated tolerances.
Derivation:
If ‘T’ is the tolerance of the ith part, the overall tolerance (T_total) is calculated as follows:
\colorbox{black}{$\textcolor{white}{\text{Total T} = \sqrt{T_1^2 + T_2^2 + \ldots + T_n^2}}$}Monte Carlo Simulation
The Monte Carlo Simulation is a computer-based method that uses randomness to simulate various possible outcomes. Engineers can see various potential results by running the simulation many times, helping them understand the likelihood of different problems.
These methods give engineers valuable insights into how changes in part sizes and tolerances might affect the final product, allowing them to make informed decisions to ensure its performance and quality.
Critical attributes in tolerance analysis
There are several vital factors that tolerance analysis brings to light which help evaluate and fine-tune design:
Sensitivity: This measures the effect of a unit change in any dimension on the final assembly dimension that is the focus of the analysis. It’s crucial in pinpointing areas of geometry that could be improved.
Contributors: This shows the share of the final assembly tolerance that each component tolerance adds. This helps in setting goals for tightening or loosening tolerances.
Tolerance Stack-Up: Understanding this helps engineers spot potential problems with assembly and function due to excessive total tolerances.
Cost Efficiency: By spotting where tolerances can be loosened without affecting functionality, it’s possible to save on manufacturing costs since tighter tolerances often mean higher production costs.
Variation Analysis: Knowing how variation in each part dimension impacts the final assembly and its operation can guide design modifications.
Manufacturing Process Capabilities: Considering what the current manufacturing processes can do is essential. Tolerances that current capabilities cannot meet will cause frequent out-of-spec situations, affecting product quality and yield.
Quality Impact: Tolerances that are too tight or too loose can harm the product’s final quality. Therefore, striking the right balance is key to ensuring a product that not only works as intended but is also of high quality.
To see how these factors play out in real scenarios, try out our engineering tolerance calculator.
The Wide-Ranging Uses of Tolerance Analysis
Tolerance analysis finds applications in various sectors thanks to its versatility and importance in maintaining quality and precision. Here’s how different industries leverage tolerance analysis:
The Automotive Industry
Tolerance analysis is crucial in ensuring the precise fit of numerous components like engine parts, suspension, and electrical systems. This precision directly enhances vehicle performance and safety.
The Aerospace Industry
With the highest requirements for precision and safety, aerospace engineering relies on tolerance analysis to ensure that aircraft components work flawlessly, even under the most extreme conditions.
Consumer Goods and Electronics
Tolerance analysis ensures the smooth assembly of intricate components, such as microchips and electrical circuits, for the electronics and consumer goods industries. The result is reliable and efficient products.
Manufacturing
Tolerance analysis assists in maintaining the quality of mass-produced goods by identifying potential issues before the manufacturing process. It’s particularly crucial in precision manufacturing, where the tiniest dimensional changes can significantly impact a product’s functionality.
Medical Equipment Design:
In the healthcare sector, tolerance analysis is vital for designing and manufacturing medical devices. Tools, implants, and diagnostic equipment must function reliably, and tolerance analysis plays a significant role in ensuring that.
Construction and Architecture:
In construction and architecture, tolerance analysis helps ensure that the various parts of a building structure or architectural model align correctly. It’s critical for structural integrity and safety, especially in modular structure design and assembly.
Robotics:
For robotics, tolerance analysis is crucial in ensuring robotic components fit together and function as intended. It’s used to ensure the precision of parts like robotic arms or components of autonomous vehicles.
Wrapping Up
Tolerance analysis is a cornerstone in engineering, fundamental to the stability and efficiency of systems and products. This process allows engineers to examine the effects of various size variations and other factors, helping to define acceptable ranges of differences that pave the way for optimal performance and functionality.
Tolerance analysis is everywhere, from cars and planes to making tools and even in factories. It’s a handy method that helps spot problems early on. This means less time fixing mistakes and more time creating awesome stuff!
At Me Virtuoso, we’re all about making these tricky concepts easy for you. Our blog posts break down complex topics, and our tools, like the Stack-Up Tolerance Analysis Calculator and Planetary Gear Simulator, allow you to learn hands-on.
Getting the hang of tolerance analysis can be a game-changer. It can help you develop better designs, make good products, and keep customers happy. If you’re a beginner or a pro in the mechanical world, understanding tolerance analysis can unlock new levels of precision and excellence in your projects.