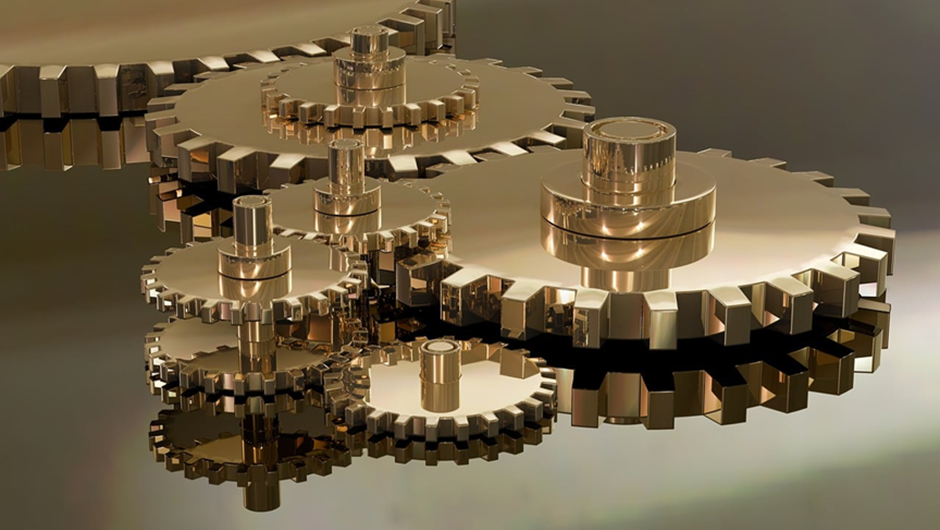
Planetary gears, also known as epicyclic gears, are a fundamental aspect of engineering and mechanics, with a unique structure that allows them to perform a wide range of tasks. Their versatility and efficiency make them invaluable in numerous fields, from automotive and industrial machinery to aerospace and robotics.
In this in-depth guide, we will simplify the concept of planetary gears and walk you through their various types, usage, and how to calculate their gear ratios. We aim to provide a clear understanding of how these fascinating gear systems function, their role in different gearboxes, and why they are essential components in various machines.
If you are in the process of developing a planetary gear, feel free to check out our Planetary Gear Simulator.
What is a Planetary Gear?
Imagine a gear system like our solar system. At the center, there’s the sun gear, and orbiting around it are smaller planet gears. All these gears are enclosed within a larger outer gear, known as the ring gear or annulus. The unique arrangement of planetary gears allows for a flexible gear ratio, enabling the sun gear, planet gear, or ring gear to be chosen as the driver or driven component.
The strength of planetary gears lies in their compact design, high load capacity, and ability to provide high torque in a small space. These gears are widely used in mechanical systems where efficiency and various gear ratios are required.
Types of Planetary Gears
Planetary gears come in various forms, each with its unique application. Let’s explore these types:
Simple Planetary Gear
The simple planetary gear setup is a perfect balance of efficiency and compactness. It is preferred in applications where space is limited, but heavy load-bearing and weight distribution are crucial.
Compound Planetary Gear
Taking a step further, the compound planetary gear includes an additional set of planet gears. Each set operates on its carrier revolving around the sun gear. This design allows excellent force distribution and high load-bearing capacity, making it suitable for applications requiring high force.
Star Gear
Star gears are designed to allow the planet gears to engage with both the sun gear and the ring gear. This configuration permits smoother operation and higher force transmission due to increased tooth engagement.
Idler Gear
In this gear system, an additional gear establishes a connection with both the sun and ring gears. This arrangement enables a change in the rotation direction without modifying the gear ratio, which is particularly useful in applications requiring bi-directional power transmission.
Differential Gear
Found primarily in vehicles, the differential gear system is crucial for distributing the engine’s power between two wheels. It allows the wheels to spin at varying speeds, facilitating smooth and safe turning while preventing wheel slippage.
Understanding the Working of Planetary Gears
When the sun gear (central gear) rotates, it triggers the movement of the planet gears (surrounding gears). These planet gears not only spin around their own axes but also revolve around the sun gear. The ring gear, the outermost gear, meshes with the planet gears, featuring inner teeth that lock onto the planet gears.
The behavior of the gear system depends on which component is stationary (held immobile) and which component is powered. Let’s explore some possible scenarios:
If the sun gear is powered while the ring gear is stationary, the planet gears will rotate around their axes and orbit the sun gear. Consequently, the planet carrier (the structure that holds the planet gears) will turn, and this rotation is our output.
If the planet carrier is powered, and the ring gear is held still, the sun gear will revolve in the reverse direction, and this rotation serves as the output.
If the sun gear is powered, and the planet carrier is held stationary, the ring gear will rotate, and this rotation constitutes the output.
The adaptability in output behavior, depending on the component that’s powered or fixed, is one of the primary advantages of planetary gear systems. They find applications in a wide array of machines and equipment, ranging from automobiles and bicycles to wind turbines. A sound understanding of the operation of these gears equips engineers with the knowledge to design machines that are not only efficient but also compact.
Calculating Gear Ratios for Planetary Gears
Determining the gear ratio for planetary gears can be accomplished through a simple formula:
Gear Ratio = (Number of Teeth on Ring Gear + Number of Teeth on Sun Gear) / Number of Teeth on Sun Gear.
Let’s break it down with an example. If a ring gear boasts 80 teeth and the sun gear possesses 20 teeth, the planetary gear ratio equals (80 + 20) / 20 = 5. This indicates that the sun gear needs to make five complete revolutions for the ring gear to accomplish a single full rotation.
Understanding the Types of Planetary Gearboxes
Planetary gearboxes utilize planetary gears to transfer force and speed from a motor to a desired output. They come in an array of varieties:
Single-stage Planetary Gearbox
This type employs a single set of gears, making it well-suited for tasks requiring high force but low speed.
Multi-stage Planetary Gearbox
Several sets of gears enable it to attain high gear ratios. Ideal for tasks demanding a lot of force and variable output speeds.
In-line Planetary Gearbox
With input and output shafts arranged in a straight line, this design provides high power, making it a favorable choice for industrial machinery due to its compact size.
Offset Planetary Gearbox
Offset input and output shafts work great for robotics and automation where space is tight.
Coaxial Planetary Gearbox
Input and output shafts are positioned on the same axis. Frequently used in automotive applications, like automatic transmissions.
Right Angle Planetary Gearbox
The distinct feature of this type is that the input and output shafts meet at a 90-degree angle, making it an excellent choice for compact designs and tasks requiring high force.
Harmonic Drive Planetary Gearbox
This unique design uses a flexible metal cup in tandem with a rigid circular spline, offering high precision and high force density. This makes it highly suited for robotics and aerospace applications.
Applications of Planetary Gears
Industrial Machinery
Planetary gears play an integral role in large machinery within factories. Their high strength and ability to handle significant force make them perfect for demanding tasks requiring substantial power.
Wind Turbines
Wind turbines employ these gears to transform wind power into electricity. The planetary gears help accelerate the generator, improving the turbine’s efficiency.
Robotics
Planetary gears are vital to the precise movements in robotics. They ensure smooth, accurate movement, enhancing the robots’ functionality.
Aerospace
In the realm of aerospace, planetary gears are a common sight. They’re utilized in spacecraft for precise movement control. Their compact size and capability to handle varying speeds make them ideal for space exploration tasks.
Conclusion
Planetary gears play a significant role in mechanical systems, much like our solar system is crucial for our existence. Their design is akin to a solar panel, and they are as vital to machines as the solar system is to our life. Understanding planetary gears and their gear ratios equips engineers with the knowledge to design efficient and compact machines.
As technology continues to improve, planetary gears will likely remain at the forefront of modern mechanical engineering. Our commitment to providing mechanical resources and calculation tools, such as the planetary gear simulator, aims to make your journey in mechanics easier and more efficient.
We strive to be your go-to platform for mechanical resources, and our goal is to keep you updated on any new developments and applications related to planetary gears, such as our Planetary Gear Simulator.
Stay connected with us for all your mechanical needs and embark on your journey to master the world of mechanics.