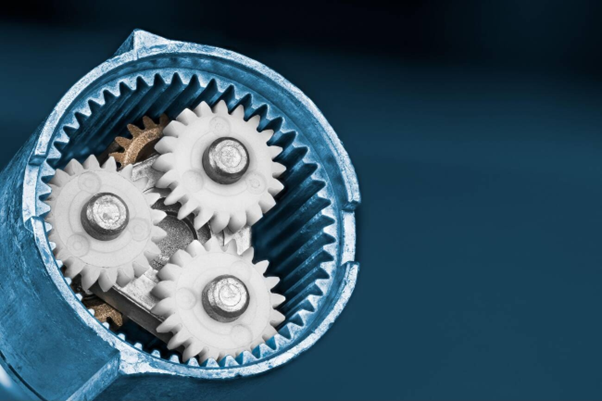
Ever heard of planetary gear systems? They might sound complex, but they’re the cool gizmos that help machines work faster and more robustly. Think of them as the power-packed heart of various devices. But here’s the catch – figuring out their gear ratios can be a bit like deciphering an ancient code.
Don’t worry; we’re here to unravel the mystery! Imagine we’re chatting over coffee rather than diving into technical jargon. We’ll walk you through the entire gear ratio thing for planetary gears step by step. Whether you’re a gear whiz or a complete newbie, we aim to make this as simple as ABC.
Exploring the Elements of a Planetary Gear System
Before delving into the gear ratio calculations, we must acquaint ourselves with the integral components forming a planetary gear system. Gaining a comprehensive understanding of each component’s distinct role will lay a robust foundation for comprehending the principles governing gear ratios.
Sun Gear:
At the heart of this intricate mechanism lies the sun gear. Strategically positioned and interlocked with the input shaft, this gear serves as the driving force behind the entire system. When power is applied to the input shaft, the sun gear sets the motion of the whole system in progress. Its rotation propels the movement of the surrounding planet gears.
Planet Gears:
Picture a celestial dance where planet gears mimic planets orbiting the sun. These gears encircle the sun gear in an orbit-like fashion. However, they don’t twirl in isolation. Typically mounted on a structure known as a ‘carrier,’ they’re meticulously designed to engage both the sun gear and the outer ring gear. Their synchronized engagement with these gears facilitates the intricate choreography of motion within the system.
Ring Gear:
Situated around the periphery, the ring gear claims the title of the largest gear within the planetary gear assembly. While the sun gear takes the lead in initiating motion, the ring gear provides the framework for support and meshing. The planet gears lock into the teeth of the ring gear, solidifying their movement patterns and ensuring harmonious synchronization.
Carrier:
Consider the carrier as the unsung hero of the ensemble—a vital but often unnoticed player. Acting as the spine of the gear set, the carrier cradles the planet gears, giving them the freedom to orbit around the central axis. Beyond that, its role extends to maintaining the precise positions of the planet gears and securing their engagement with both the sun gear and the ring gear. This pivotal role transforms the carrier into a conduit for transmitting force and directing the nuanced movements within the planetary gear system.
In numerous gear systems, we encounter scenarios where one component remains stationary while others partake in orchestrated movement, yielding patterns we can predict. Yet, it’s important to note that exceptions do exist. For instance, input and output can be intertwined in the context of an automobile’s automatic transmission. This unique interlinking causes all components—the sun, ring, or planet gears—to move in tandem, leading to a captivating display of intricate behaviors.
Exploring Gear Ratios in Planetary Gear Systems: A Mathematical Journey
Let’s begin by looking at how gears work. Imagine you have two gears – one is the sun gear, and the other is the ring gear. Each of these gears has some teeth on them. When we add the teeth on the sun gear and the ring gear, we get the total number of teeth on the planet gears. For example, if the sun gear has 20 teeth and the ring gear has 60 teeth, then the planet gears together have 80 teeth.
And guess what? We have a tool, our unique gear simulator, that makes these calculations super easy. Just one click, and you’ve got the answer!
Different Situations, Different Math
Now, let’s talk about different scenarios in planetary gears. Imagine you have gears making things happen (we call this the driver gear, D) and gears going along for the ride (we call this the driven gear, d). Here’s where the math comes in: we will use equations to figure things out. Let’s jump right in:
Carrier as the Driver
When the carrier (C) takes the reins of motion while the sun gear remains steadfast, our equation materializes as follows:
\textcolor{white}{\colorbox{black}{$Gear Ratio = \frac{R}{P}$}}
- R: Teeth count on ring gear
- P: Teeth count on planet gear
Thus, if R = 60 and P = 80, we unveil Gear Ratio = 60 / 80 = 0.75 or 3:4.
Carrier as the Recipient
In a setting where the sun gear (S) propels the action while the ring gear (R) stands still, the equation assumes the form:
\textcolor{white}{\colorbox{black}{$Gear Ratio = \frac{P}{S}$}}
- S: Teeth count on sun gear
- P: Teeth count on planet gear
Given P = 80 and S = 20, Gear Ratio = 80 / 20 = 4 or 4:1.
Carrier at a Standstill
When the carrier (C) remains at rest, and the ring gear (R) orchestrates the motion, we express our equation as:
\textcolor{white}{\colorbox{black}{$ Gear Ratio = \frac{S}{R}$}}
- S: Teeth count on sun gear
- R: Teeth count on ring gear
Should S = 20 and R = 60, Gear Ratio = 20 / 60 = 1/3 or 1:3.
Calculating Gear Motion in Planetary Systems
Picture a planetary gear system as a choreography of moving parts. To decipher this dance, we wield a potent formula harmonizing elements crucial to the system’s rhythm. This formula intertwines the number of teeth on the sun gear (S) and the ring gear (R) with the speeds (often measured in revolutions per minute, or rpm) of the ring gear (ωr), the carrier arm (ωa), and the sun gear (ωs). Behold the equation:
\textcolor{white}{\colorbox{black}{$\cfrac{{S}}{{-R}} = \cfrac{{\omega_r – \omega_a}}{{\omega_s – \omega_a}}$}}
Breaking it down:
- S signifies the teeth count on the Sun gear,
- R represents the teeth count on the Ring gear,
- ωr captures the velocity of the ring gear,
- ωa encapsulates the pace of the carrier arm, and
- ωs portrays the swiftness of the sun gear.
Now, let’s unravel the magic this formula brings. Plug in these values, and we can foresee gears working together like a symphony, uncovering how a planetary gear system ticks.
And that’s not all—brace yourself for more excitement. This knowledge empowers engineers to shape custom gear systems for various jobs. Armed with this formula, they steer through industries and tasks, crafting with precision and imagination.
The Role of Gear Ratios in Different Industries
Gear ratios are silent heroes, enhancing efficiency and output across diverse sectors. Here’s a glimpse into their pivotal roles:
Manufacturing Equipment:
Think of machines like drill presses or milling machines. These workhorses harness gear ratios to regulate rotation speed and power. This precision ensures meticulous cuts and shapes, shaping products with finesse.
Transportation Systems:
Consider conveyor belts in bustling warehouses. They dance to the rhythm of gear ratios, orchestrating speed to facilitate the seamless movement of goods. This choreography optimizes productivity.
Mining Equipment:
Visualize colossal excavators and loaders in mining operations. These behemoths harness gear ratios to allocate power efficiently. The result? They triumphantly tackle hefty loads with grace and effectiveness.
Construction Equipment:
Shift your focus to construction sites. Cranes stretch towards the sky and concrete mixers whirl. Behind their might is the magic of gear ratios, essential for heavy lifting and precise mixing.
Across these domains, gear ratios act as a catalyst. They elevate machine performance, infuse productivity, and orchestrate operations with elegance. As technology marches forward, gear ratios remain the unsung pioneers of innovation and efficiency.
Final Thoughts
Planetary gear ratios are the silent force propelling mechanical systems in vehicles, factories, and construction sites. These ratios enable these systems to function and fine-tune their performance, ensuring efficiency and reliability.
Understanding gear ratios is crucial for mechanical engineering students and professionals alike. Our Planetary Gear Simulator simplifies these complex concepts, allowing for practical application without the need for memorization.
Explore our mechanical blogs for insightful articles and expert perspectives on mastering mechanics. We’re not just a resource; we’re your companion on the journey to mastering mechanics. Stay connected for all your mechanical needs.
FAQs
1. How can engineers be sure that the chosen gear ratios will meet the needs of their applications?
Engineers can use simulation and analytical tools to model and test gear systems. This allows them to ensure that the chosen gear ratios will work optimally for their specific applications. Check our Planetary Gear Simulator
2. What are the advantages of using a simulation tool to study planetary gear systems?
Simulation tools allow engineers to explore various gear combinations and predict system performance without the need for physical prototypes. This can save both time and resources in the design and testing process.
3. How do gear ratios affect the speed and torque of a gear system?
Gear ratios have a significant impact on a gear system’s speed and torque. Higher gear ratios typically result in greater torque but slower speeds, while lower gear ratios usually lead to less torque but higher speeds. This relationship allows engineers to fine-tune the balance of speed and torque in a system to suit specific needs.