Planetary gear simulators, also known as epicyclic gear trains, have long been a staple in many industries where efficient power transmission is crucial. From automotive transmissions to industrial machinery, these gear systems play a vital role in delivering high torque and smooth operation. However, for many, the inner workings of planetary gear simulators remain a mystery. In this article, we aim to demystify these powerful mechanisms and uncover the secrets behind their efficiency.
Understanding the Basics of Planetary Gear Simulators
To comprehend the efficiency and power transmission capabilities of planetary gear simulators, it is essential to start with the basics. At its core, a planetary gear system consists of three main components: a sun gear, planet gears, and a ring gear. The sun gear is positioned at the center, surrounded by multiple planet gears, which are meshed with both the sun gear and the ring gear.
Power Transmission and Torque Amplification
One of the key advantages of planetary gear simulators is their ability to transmit power efficiently. This efficiency is achieved through torque amplification, which is the result of distributing the torque load among multiple planet gears. As the sun gear transfers power to the planet gears, it creates a rotational force that is transmitted to the ring gear. This distributed power transmission reduces the load on individual gears, minimizing wear and increasing overall efficiency.
The Role of Gear Ratios
The efficiency and power transmission capabilities of planetary gear simulators are further influenced by gear ratios. By adjusting the size of the gears, different gear ratios can be achieved, allowing for variations in speed, torque, and direction of rotation. Gear ratios play a crucial role in optimizing power transmission for specific applications. For instance, in automotive transmissions, different gear ratios are used to provide the ideal balance between acceleration and fuel efficiency.
Efficiency and Power Loss
While planetary gear simulators are known for their efficiency, it is essential to acknowledge that some power loss does occur during operation. Power loss can be attributed to factors such as friction, gear meshing, and bearing drag. However, advancements in gear design, lubrication, and materials have significantly reduced these losses over the years. Today, planetary gear simulators can achieve efficiency levels exceeding 95%, making them a reliable choice for power transmission applications.
Applications and Benefits
Planetary gear simulators find application in various industries, including automotive, aerospace, robotics, and industrial machinery. Their benefits extend beyond efficient power transmission. These benefits include:
- Compact Size: The design of planetary gear simulators allows for a high gear reduction ratio within a compact space, making them ideal for applications with limited space.
- High Torque Capacity: The distributed power transmission in planetary gear systems enables them to handle high torque loads, making them suitable for heavy-duty applications.
- Smooth Operation: The multiple-gear meshing in planetary gear simulators results in reduced vibration and noise levels, ensuring smoother operation.
In the following sections, we will delve deeper into the inner workings of planetary gear simulators and explore their significance in mechanical engineering.
The Role of Planetary Gear Simulators in Mechanical Engineering
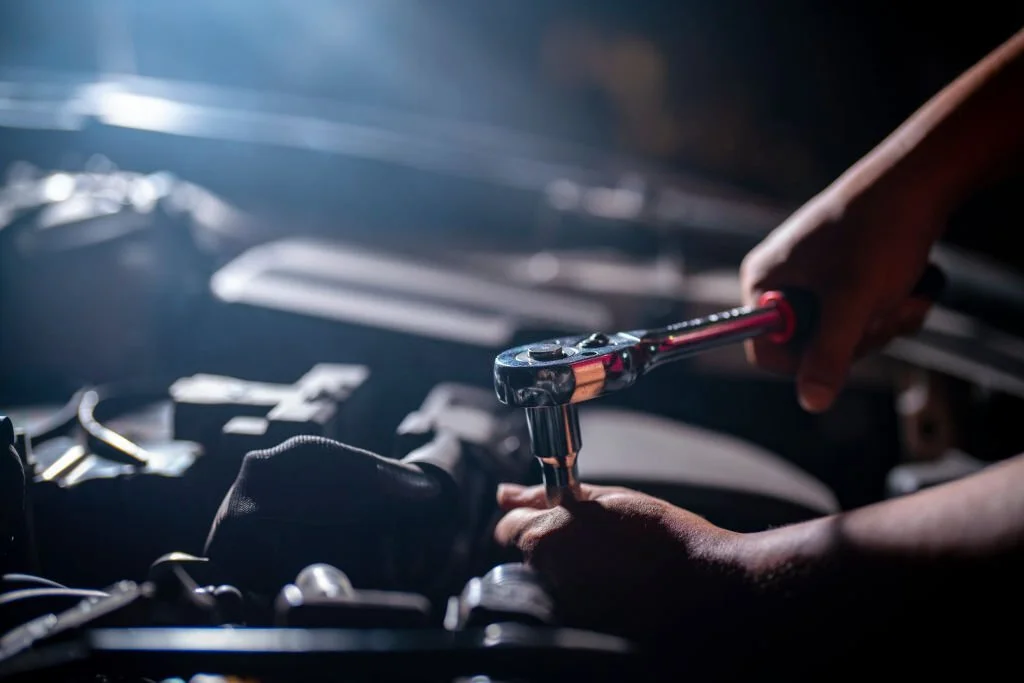
Automotive Industry
The automotive industry is one of the primary sectors where planetary gear simulators find extensive use. They are an integral part of automatic transmissions, providing efficient power transmission and torque multiplication. In automatic transmissions, planetary gear sets allow for seamless shifting between different gear ratios, enabling smooth acceleration and optimal fuel efficiency. The compact size and high torque capacity of planetary gear simulators make them ideal for fitting within the limited space constraints of automotive applications.
Aerospace and Robotics
Planetary gear simulators also play a crucial role in the aerospace and robotics industries. In aerospace applications, these gear systems are utilized in aircraft engines, landing gear mechanisms, and auxiliary power units. The ability to handle high torque loads, coupled with their compact size, makes planetary gear simulators well-suited for aircraft propulsion systems. In robotics, they are employed in robotic arms, joints, and manipulators, enabling precise and efficient movement.
Industrial Machinery
In the realm of industrial machinery, planetary gear simulators are widely employed for various applications. They are used in heavy machinery such as cranes, excavators, and mining equipment, where high torque and durability are essential. The robust design and torque multiplication capabilities of planetary gear systems allow for efficient power transmission in demanding industrial environments. Additionally, their smooth operation and reduced vibration contribute to enhanced overall performance and longevity of the machinery.
Advancements in Planetary Gear Technology
As technology continues to advance, so does the design and capabilities of planetary gear simulators. Engineers and researchers are constantly exploring innovative approaches to improve efficiency, reduce power loss, and enhance the performance of these gear systems. Some notable advancements in planetary gear technology include:
- Material Selection: The use of advanced materials, such as high-strength alloys and composites, improves the durability and load-carrying capacity of gear components, leading to increased efficiency and longevity.
- Lubrication Systems: Optimized lubrication systems, including the use of high-performance lubricants and enhanced cooling mechanisms, help reduce friction and minimize power losses within the gear system.
- Gear Design Optimization: Advanced computer-aided design (CAD) and simulation tools enable engineers to optimize gear designs, ensuring optimal tooth profiles, contact patterns, and load distribution, thereby improving overall efficiency.
These advancements in planetary gear technology contribute to the continual improvement of mechanical systems across various industries, enabling more reliable and efficient power transmission.
In conclusion, planetary gear simulators are powerful mechanisms that play a crucial role in efficient power transmission. Their ability to handle high torque loads, compact size, and smooth operation makes them indispensable in industries such as automotive, aerospace, robotics, and industrial machinery. As technology progresses, further advancements in gear design and materials will continue to enhance the efficiency and performance of planetary gear simulators, driving innovation in mechanical engineering.
Advantages of Planetary Gear Simulators
The use of planetary gear simulators in mechanical engineering offers numerous advantages over traditional analytical methods and physical prototyping. These simulators provide engineers with advanced tools to simulate, analyze, and optimize gear systems, resulting in improved design efficiency, reduced costs, and enhanced overall reliability. Let’s explore some of the key advantages in more detail:
1. Cost and Time Savings
Designing and prototyping physical gear systems can be time-consuming and expensive. However, by utilizing simulators, engineers can quickly evaluate numerous design iterations without incurring significant costs or lengthy prototyping cycles. This accelerates the development process and reduces overall project costs, allowing engineers to allocate resources more effectively.
Gear Design and Analysis Software provides a comprehensive set of tools to simulate and analyze planetary gear systems, significantly reducing the need for physical prototypes and associated expenses.
2. Design Optimization
Simulators provide engineers with a comprehensive understanding of how different design parameters affect the performance of planetary gear systems. By leveraging simulation results, designers can fine-tune gear ratios, tooth profiles, lubrication conditions, and other factors to achieve optimal system performance. This iterative optimization process leads to improved efficiency, reduced noise, and increased durability.
Fine-tuning and Optimization using simulation tools allows engineers to explore various design configurations and quickly identify the most suitable parameters for achieving desired performance objectives.
3. Performance Analysis
Simulators enable engineers to analyze the dynamic behavior of planetary gear systems under various load conditions. By visualizing the motion, torque distribution, and mechanical stresses, engineers can identify potential issues and ensure the system operates within safe operating limits. This insight allows for the early detection and resolution of design flaws, preventing costly failures in the field.
Performance Analysis using simulators provides engineers with detailed information on torque output, gear ratios, power losses, and overall system efficiency. This analysis aids in optimizing gear systems for specific performance requirements.
4. Education and Training
Planetary gear simulators also serve as valuable educational tools. They allow students and aspiring engineers to gain hands-on experience with complex gearing systems in a controlled environment. By experimenting with different gear configurations and observing the resulting motion, students can deepen their understanding of gear mechanics and apply theoretical knowledge to practical scenarios.
Planetary Gear Simulators provide a virtual playground for educational purposes, helping individuals grasp the fundamental principles of gear systems and their applications in various industries.
By harnessing the power of planetary gear simulators, engineers can unlock new possibilities in gear system design, analysis, and optimization. These simulators empower engineers to make informed decisions, reduce development time, and ensure the reliability and performance of gear systems.
In the next section, we will provide a step-by-step tutorial on how to effectively use planetary gear simulators, guiding engineers and gear enthusiasts through the process of analyzing, optimizing, and designing planetary gear systems.
Step-by-Step Tutorial: Analyzing, Optimizing, and Designing Planetary Gear Systems
In this section, we will walk you through a step-by-step tutorial on how to effectively use planetary gear simulators for analyzing, optimizing, and designing gear systems. Whether you are a mechanical engineer, a student, or a gear enthusiast, this tutorial will provide you with practical guidance on harnessing the power of simulators to unlock the full potential of your gear designs. Let’s get started!
Step 1: Choosing the Right Planetary Gear Simulator
The first step in utilizing a planetary gear simulator is selecting the appropriate software for your needs. There are several options available in the market, each with its own features and capabilities. It is essential to choose a simulator that aligns with your specific requirements and provides the necessary tools for accurate analysis and optimization.
Gear Design and Analysis Software offers a wide range of simulators tailored for different applications, from basic gear calculations to advanced multi-body dynamic simulations. Consider factors such as ease of use, available features, compatibility with your computer system, and the level of accuracy required for your project.
Step 2: Defining the Gear System Parameters
Once you have selected the appropriate planetary gear simulator, the next step is to define the gear system parameters. This includes specifying the number of gears, gear tooth profiles, gear ratios, and other relevant parameters that define the geometry and kinematics of the gear system.
Gear System Parameters play a crucial role in determining the performance characteristics of the gear system. Accurate input of these parameters is essential for obtaining reliable simulation results.
Step 3: Analyzing Gear Behavior
With the gear system parameters defined, it’s time to analyze the behavior of the gear system using the simulator. This step involves setting up the simulation environment, applying appropriate loads and constraints, and running the simulation to obtain key performance metrics.
Performance Analysis provides insights into torque distribution, power losses, gear efficiency, and other critical factors that influence the performance and reliability of the gear system. Analyzing these metrics helps identify potential issues and optimize the gear design for enhanced performance.
Step 4: Fine-Tuning and Optimization
Based on the analysis results, the next step is to fine-tune and optimize the gear system design. This involves making adjustments to various parameters such as gear ratios, tooth profiles, lubrication conditions, and other factors to achieve the desired performance objectives.
Fine-tuning and Optimization using the simulator allows engineers to explore different design configurations and evaluate their impact on the gear system’s performance. This iterative process helps refine the design for improved efficiency, reduced noise, and increased durability.
Step 5: Validating the Design
Once the optimization process is complete, it is crucial to validate the gear system design using the simulator. This involves conducting additional simulations to verify the performance improvements achieved through optimization and ensure that the design meets the desired specifications.
Design Validation enables engineers to assess the reliability and functionality of the gear system before proceeding to the physical prototyping stage. It helps identify any remaining design issues and allows for further refinements if necessary.
Step 6: Documentation and Reporting
Finally, it is essential to document and report the findings of the simulation process. This includes capturing relevant data, generating comprehensive reports, and communicating the results to stakeholders and colleagues. Clear documentation ensures that the design rationale, simulation settings, and performance metrics are well-documented for future reference.
Documentation and Reporting help maintain a record of the design process and facilitate knowledge sharing within the engineering team. It also aids in troubleshooting, design improvement, and comparison of different design iterations.
By following these step-by-step guidelines, you can effectively utilize planetary gear simulators to analyze, optimize, and design gear systems with precision and efficiency. These simulators empower engineers to explore a wide range of design possibilities, reduce development time, and ensure the reliability and performance of gear systems.
In the next section, we will provide a list of recommended planetary gear simulators and resources to further enhance your understanding of gear system analysis and design.
Recommended Planetary Gear Simulators and Additional Resources
Planetary gear simulators play a crucial role in the design, analysis, and optimization of gear systems. They provide engineers and enthusiasts with powerful tools to simulate and visualize the behavior of planetary gears in a virtual environment. In addition to the popular simulators mentioned below, there is another noteworthy planetary gear simulator available: the Planetary Gear Simulator from ME Virtuoso.
The Planetary Gear Simulator from ME Virtuoso offers a user-friendly interface and advanced features that allow you to explore and understand the dynamics of planetary gear systems. With this simulator, you can dynamically modify system parameters such as the number of teeth, speed, and gear ratios while visualizing the motion of the gears in real-time. The simulator also automatically calculates dimensions, speed ratios, and torque ratios, providing valuable insights into the performance of the gear system.
By using the Planetary Gear Simulator from ME Virtuoso, you can gain a deeper understanding of how changes in parameters affect the behavior of planetary gears. This simulator enables you to experiment with different gear configurations, optimize performance, and make informed design decisions.
In combination with other simulators mentioned in this article, the Planetary Gear Simulator from ME Virtuoso expands your options for exploring and analyzing planetary gear systems. It provides an intuitive platform for learning, designing, and simulating gear systems, contributing to your expertise in gear design and analysis.
Whether you are an engineer, a student, or a gear enthusiast, incorporating the Planetary Gear Simulator from ME Virtuoso into your toolkit enhances your ability to understand and optimize the performance of planetary gear systems. By leveraging this simulator along with other resources, you can unlock new possibilities and achieve excellence in gear design.
Planetary Gear Simulators
Gearotic Motion: Gearotic Motion is a comprehensive gear design and simulation software that offers advanced features such as multi-body dynamic simulations, customizable gear profiles, and real-time visualization. It provides a user-friendly interface and powerful tools for analyzing and optimizing planetary gear systems.
MDESIGN: MDESIGN is a professional engineering software suite that includes modules for gear design and analysis. It offers a range of functionalities for calculating gear parameters, simulating gear behavior, and optimizing gear system performance. MDESIGN provides accurate results and supports various industry standards.
KISSsoft: KISSsoft is a widely used software for gear and transmission design. It offers comprehensive capabilities for gear geometry calculations, load analysis, and optimization. KISSsoft also integrates with other engineering software tools, allowing for seamless data exchange and collaboration.
ADAMS: ADAMS (Automatic Dynamic Analysis of Mechanical Systems) is a powerful multibody dynamics simulation software. While not exclusively dedicated to gear systems, ADAMS provides advanced simulation capabilities that can be used to analyze and optimize the behavior of planetary gear systems within larger mechanical systems.
Additional Resources
AGMA Standards: The American Gear Manufacturers Association (AGMA) publishes a range of standards and technical publications related to gear design, analysis, and manufacturing. These resources provide in-depth guidelines and best practices for gear system engineering.
Textbooks on Gearing: There are several authoritative textbooks available on the subject of gearing that cover various aspects of gear system analysis and design. Some recommended titles include “Handbook of Practical Gear Design” by Dudley and “Gear Design Simplified” by Franklin D. Jones.
Online Gear Design Courses: Online platforms and educational websites offer specialized courses and tutorials on gear system analysis and design. These courses provide structured learning opportunities and hands-on exercises to enhance your skills and understanding of gear engineering principles.
Gear Design Forums and Communities: Engaging with online forums and communities dedicated to gear design can be a valuable resource for knowledge sharing and problem-solving. Platforms like Gear Technology and Eng-Tips provide forums where engineers and gear enthusiasts can ask questions, exchange ideas, and learn from experienced professionals.
By exploring these simulators and additional resources, you can gain a deeper understanding of gear system analysis and design concepts and further enhance your skills in this field.
In conclusion, planetary gear simulators offer powerful tools for analyzing, optimizing, and designing gear systems with precision and efficiency. By following the step-by-step tutorial provided earlier and utilizing the recommended simulators and resources, you can unlock the full potential of your gear designs and ensure the reliability and performance of your gear systems.
Remember to always consult the specific documentation and user guides provided by the software developers for detailed instructions on using the simulators effectively. Happy gear designing!