3D Printed Planetary Gear Reducer for NEMA 17 Stepper Motor
3D printed Cycloidal Drive for a NEMA 17 stepper motor.
- I designed and printed a planetary gear speed reducer. I made two types of reducers.
- The first is a simple 1 stage reducer, which produces a theoretical reduction of 4.28.
- The second is a 2-stage reducer, which produces a theoretical reduction of 18.3.
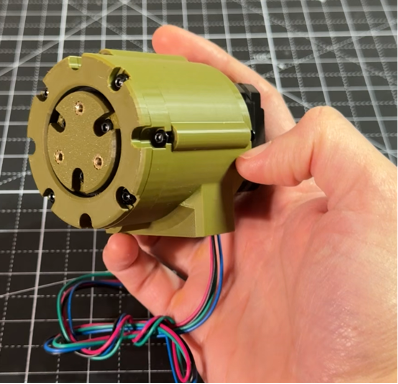
Design Process
I used the Planetary Gear Simulator to help me make design choices that would best fit my application. I wanted a compact design, and I wanted to use the reducer for a NEMA 17 stepper motor. The size of the stepper motor gave an indication of how large the reducer should be. With this in mind, I tried to minimize the speed reduction, in order to maximize the torque output. One other initial constraint is that I knew that I wanted the ring gear of the planetary reducer to be fixed, as this makes mechanical design more straight forward.
After playing with the parameters in the simulator, I landed on the values below:
Ring teeth = 46
Planet Teeth = 16
Sun teeth = 14
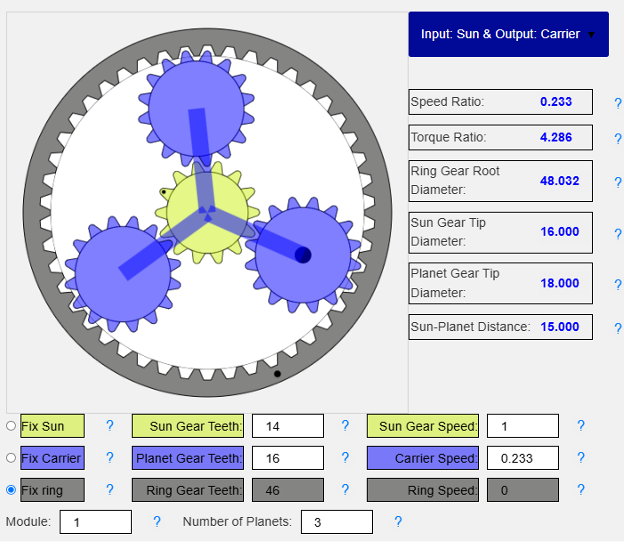
The Planetary Gear Simulator automatically calculates the reduction ratio, however, we can verify this by applying the reduction ratio equation below. Note this equation is valid when the Ring Gear is fixed.
These parameters would give a theoretical speed reduction of 30:7, or 4.28. Additionally, considering a Gear Module = 1 (anything smaller than this would produce teeth too small to 3D print), we would have a ring root dimeter of 48mm. This looked reasonable to me, the NEMA 17 casing is 42x42mm, so the ring diameter wouldn’t be too much bigger than this.
CAD
After having landed on the desired parameters, I needed to move to CAD to start designing the Planetary Gear Reducer.
There are multiple way to create the gear profiles, however, the easiest is using our Gear Generator tool. Here I just need to set three parameters and the profiles is generated as DXF file. This can be easily imported into the desired CAD software.
After having the profiles imported into SolidWorks, I started designing the different components and creating the assembly. I tried to minimize the number of hardware needed, but at the same time, I wanted to achieve smooth motion so I included ball bearing where needed.
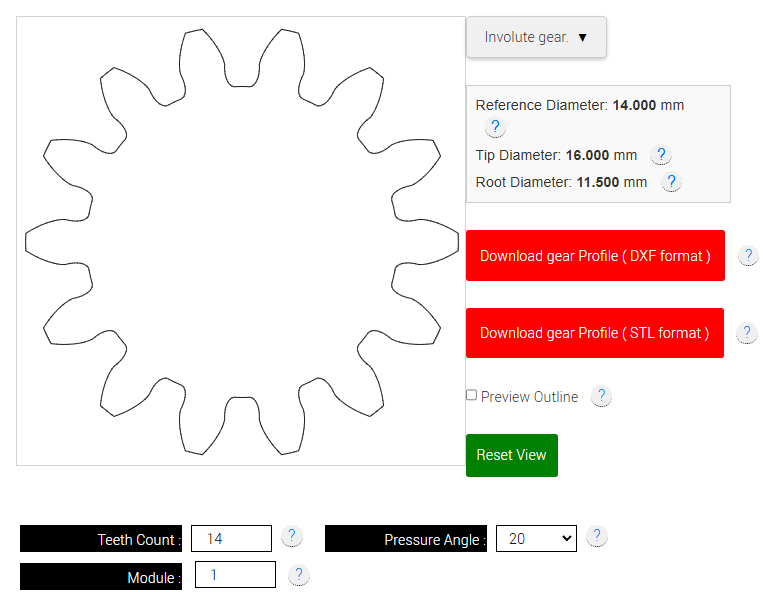
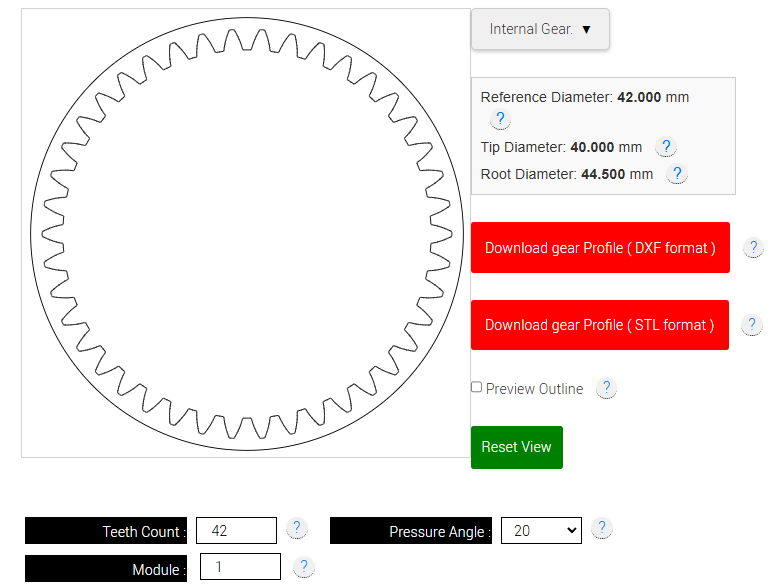
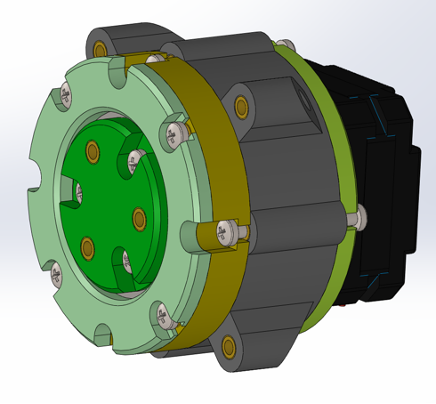
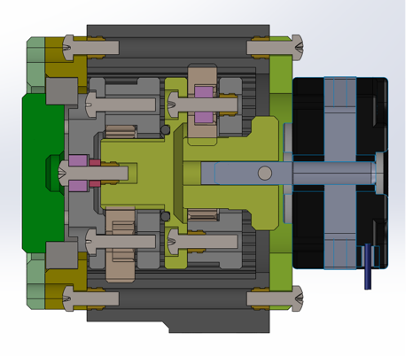
After having the profiles imported into SolidWorks, I started designing the different components and creating the assembly. I tried to minimize the number of hardware needed, but at the same time, I wanted to achieve smooth motion so I included ball bearing where needed.
Below you can see the final result. We make use of two size of ball bearing, and only M3 screws of different lengths. I also designed the parts to be used with M3 heat inserts, as I believe this to be a more elegant solution than screwing directly into the plastic.
Testing & Evaluation
I tested the torque output of the Planetary Gear drive and compared it to the torque output of the motor alone.
I designed a stand and mounted it to 2020 aluminum extrusions. Also used a 3D printed lever and mounted it to the motor output plate. Then pressed it against a kitchen scale and recorded the max reading. Considering the scale readings and the length of the lever, I was able to calculate the torque output of the motor, and of the motor with the reducers.
The results are shown below:
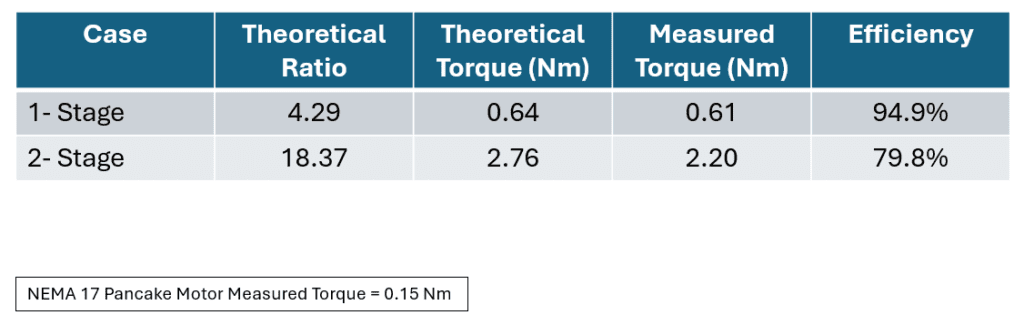
Looking at the 1-stage drive, we see that we get a reduction of 4. Comparing this to the theoretical reduction of 4.29, we see that are able to achieve an efficiency of over 90%
In the case of the 2-stage drive, the measured reduction is 14.6, which equates to an efficiency of close to 80%. It’s important to note that due to the high torques, during the 2-stage testing the 3D printed bracket started to bend. I believe with a more rigid setup higher torques could be achieved.
Conclusion
The designed planetary gear drives are able to achieve high efficiencies. These were designed with simplicity in mind and would be a great addition to high-torque and low-speed applications.
The STL files are available for download if you want to 3D print these for your project. STP files are also published in the Shop page and can be used for modification or for more detailed inspection in any CAD software.
Feel free to check out our Planetary Gear Simulator and Gear Generator tools if you want to design your own Planetary Gear drive.